インサーキットテスタとは
プリント回路板の実装不良を電気的に検出する検査装置。
検査対象基板のポイントにプローブを接触させ 微小な 測定信号(電圧または電流)を印加し 電圧・電流を 測定することで、「電子部品と基板との接続信頼性」 「実装された個々の電子部品の定数」「極性」などを検査する。
検査対象基板に負荷をかけることなく、目視検査・AOI・X線検査では発見困難な不良を 確実に検出できる。
絶縁板の表面や内部に銅などの金属で 微細な配線を形成したプリント配線板(生基板)に種々の電子部品を搭載し、 ハンダで接続されて電子回路として動作するようになったもの。 実装基板。
![]()
電子機器の内部には必ず電子回路基板が入っている。電子機器が正しく機能するためには電子回路基板が正常に動作する必要がある。 電子回路基板は、電子部品がプリント配線板(基板)に正しく実装され、電源が供給されることにより動作が可能となる。 この電子部品が実装された状態の基板を検査するのがインサーキットテスタである。
インサーキットテスタは、電子部品と基板との接続信頼性を検査することが目的であり、その手段として、実装された電子部品(抵抗器・コンデンサ等)の定数、ダイオード特性などを測定することにより実装基板の良否を判定する装置である。 MDA(Manufacturing Defect Analyzer)と呼ばれる検査装置も広義においてはインサーキットテスタに含まれる。
一般社団法人日本電気計測器工業会(JEMIMA)![]()
主な検査内容
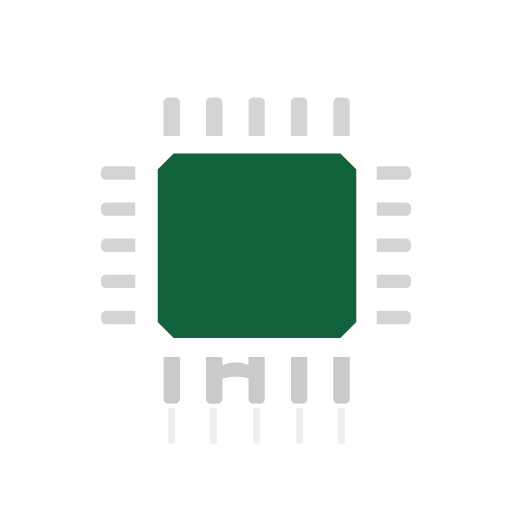
はんだショート(短絡)
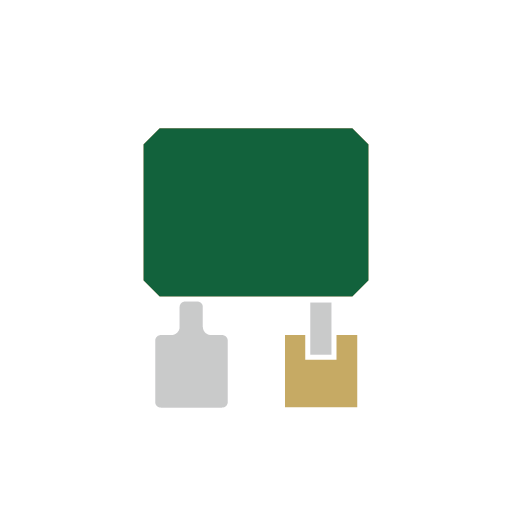
オープン(未はんだ)
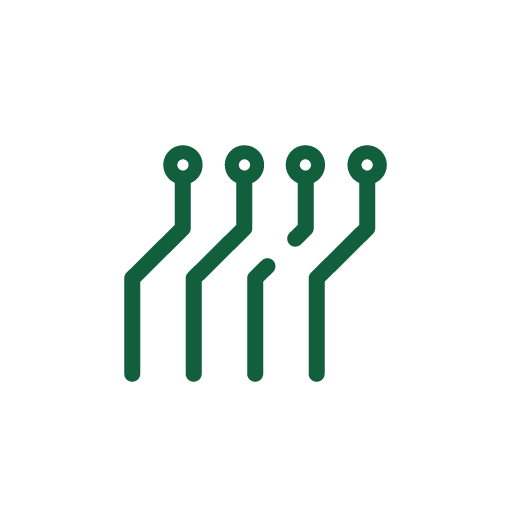
パターン断線
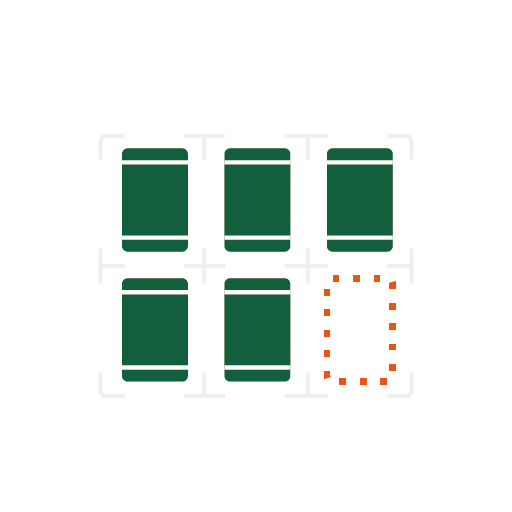
部品の欠品
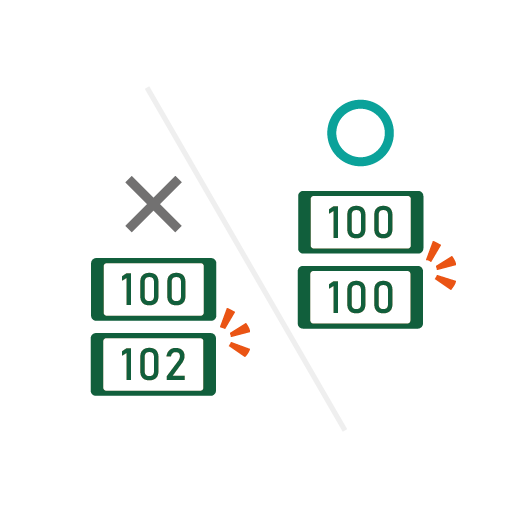
部品の定数間違い
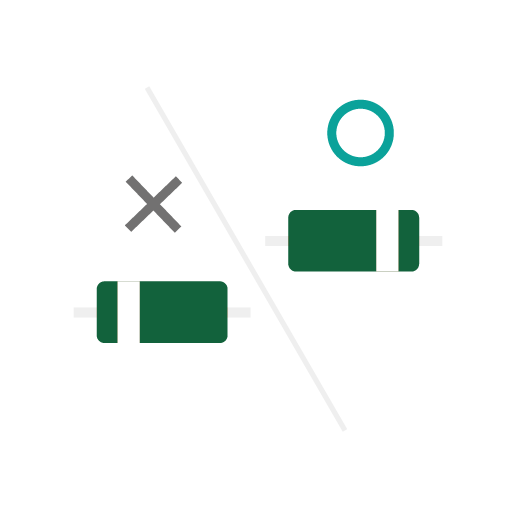
極性のある部品の逆実装
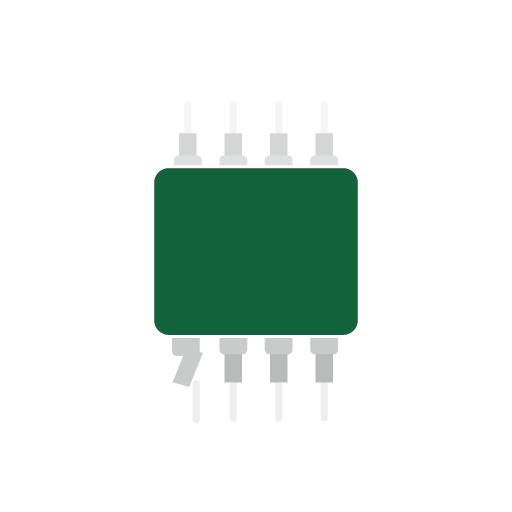
IC・コネクタのリード浮き
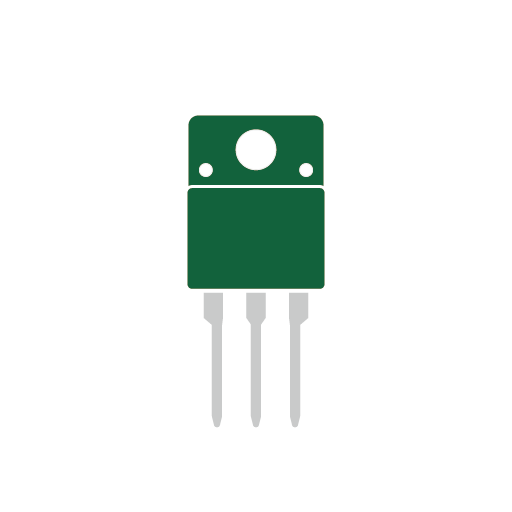
デジタルトランジスタ、
FET、
フォトカプラの動作確認
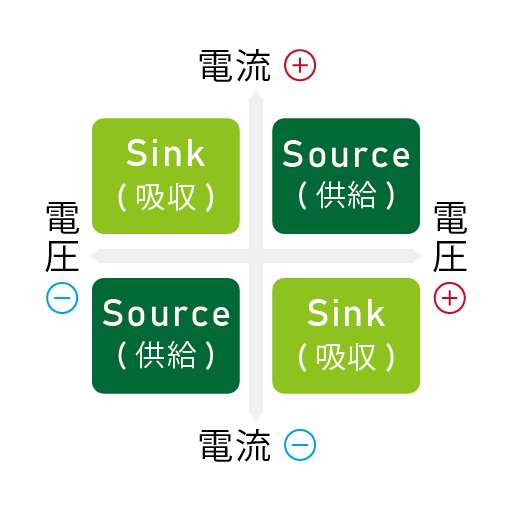
簡易ファンクション検査
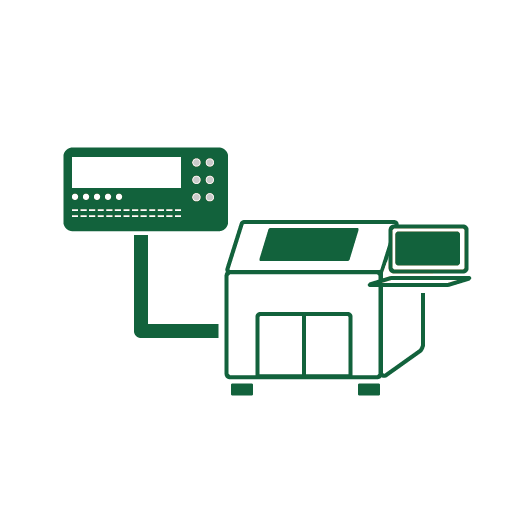
外部機器を接続した特殊検査
測定原理
DC(直流)測定
対象物にDC定電圧またはDC定電流を印加し、オームの法則より抵抗値を算出する。
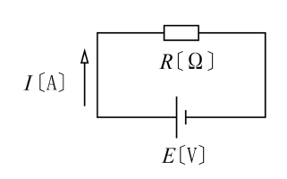
AC(交流)測定
抵抗およびコイル、コンデンサによって構成された回路網にAC定電圧を印加し、印加信号と計測信号の位相差から抵抗値、容量性負荷値、誘導性負荷値、ならびにインピーダンスを算出する。
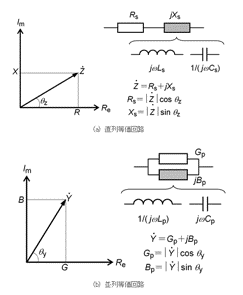
ダイオード測定
順方向にDC定電流を印加し、Vf(順方向電圧)を測定。
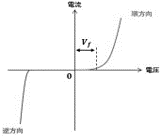
ツェナーダイオード測定
逆方向にDC定電流を印加し、Vz(ツェナー電圧)を測定。
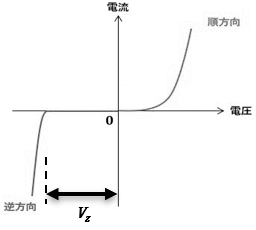
トランジスタ測定
ベース-エミッタ間、コレクタ-エミッタ間にDC定電流を印加し、コレクタ-エミッタ間電圧を測定。電圧値が0.3V以下であれば正常、超過であれば不良(ONしていない)と判定。
ベース-エミッタ間に定電流を印加後、コレクタ-エミッタ間に1.0Vを印加、電流値を測定し、Ic / Ib より hFE(直流電流増幅率)を測定。
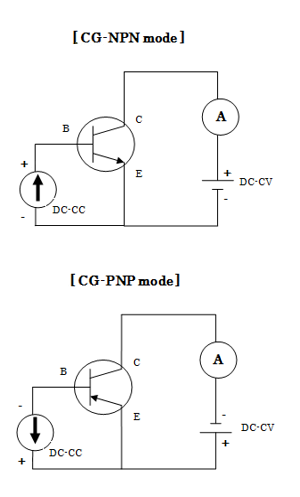
IC測定
隣接するリード間のショートチェック
隣接するリード間へ、DC定電流を印加し、リード間の抵抗値が、しきい値未満であればFAILと判定。
ICグランド~各リード間のVf測定
GND(グランド)とICの各リードへDC定電流を印加し、内部に形成されている寄生ダイオードのVfを測定。
ICオープンテストシステム(タカヤオリジナル)
詳細はこちら
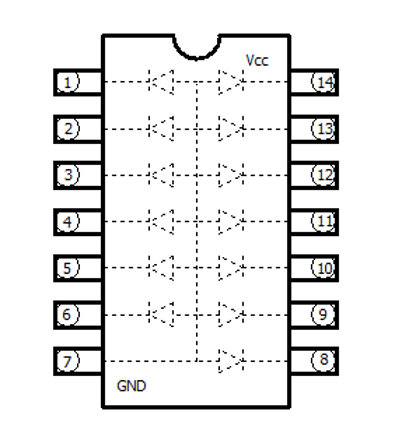
インサーキットテスタの種類
治具式テスタ
プレス機構によって、検査治具の全プローブを基板の所定テストポイントに同時接触させ、計測ラインをスキャナ部(リレー回路)で切り替えながら、各電子部品の検査を実行する。
治具は「ピンボード」「フィクスチャ」とも呼ばれ、検査対象基板ごとに製作する必要がある。 主に、大量生産基板の検査に用いられる。
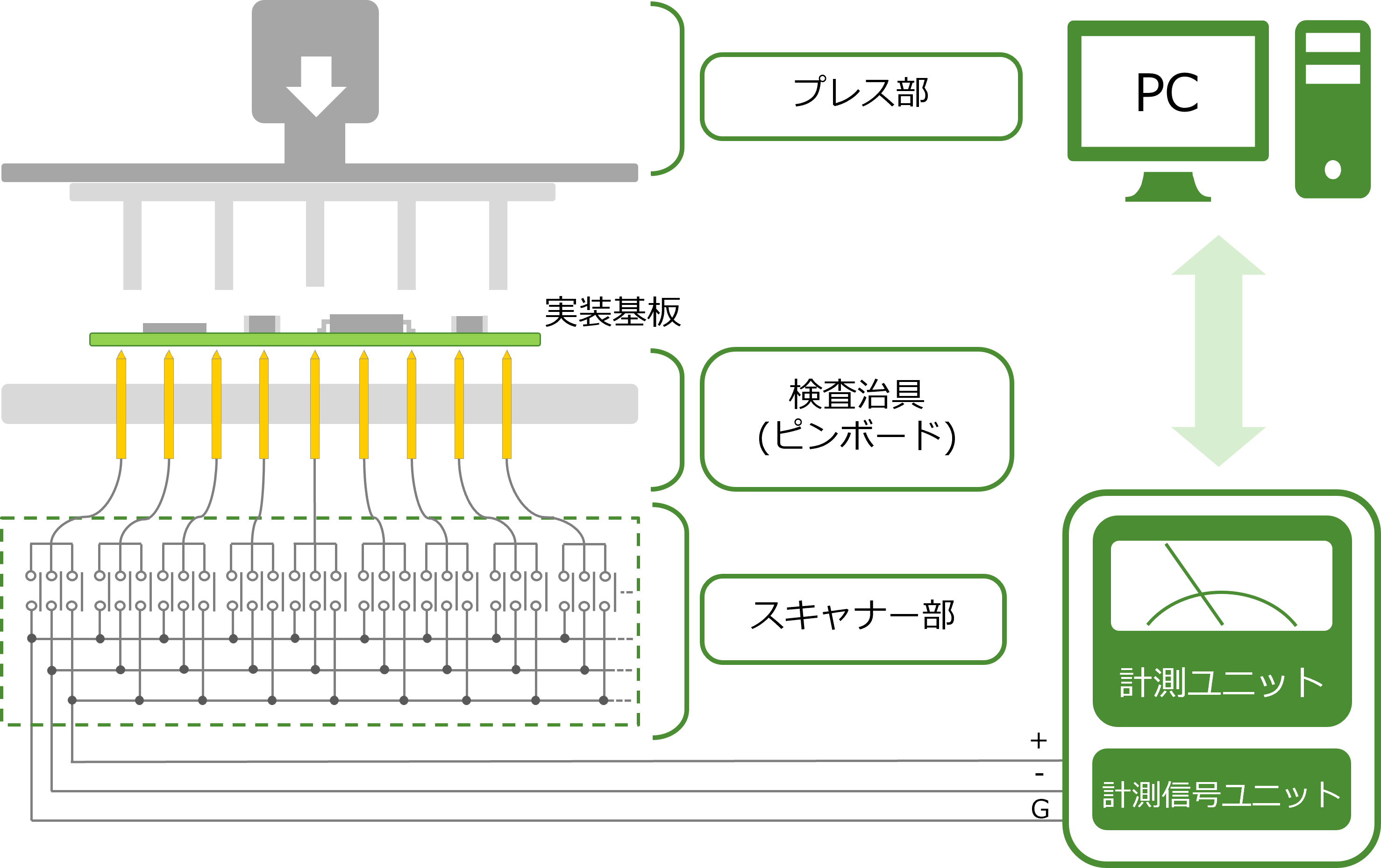
フライングプローブテスタ
複数のアームを、基板上の任意のポイントに移動させてプロービングを行う。
治具不要で、検査プログラムの入れ替えのみで段取り替えが可能なため、特に多品種・少量生産基板の検査に適している。 テストポイント座標も任意に変更できるので、設計変更への対応も容易で、試作基板の実装検査や、不良解析でも利用されている。
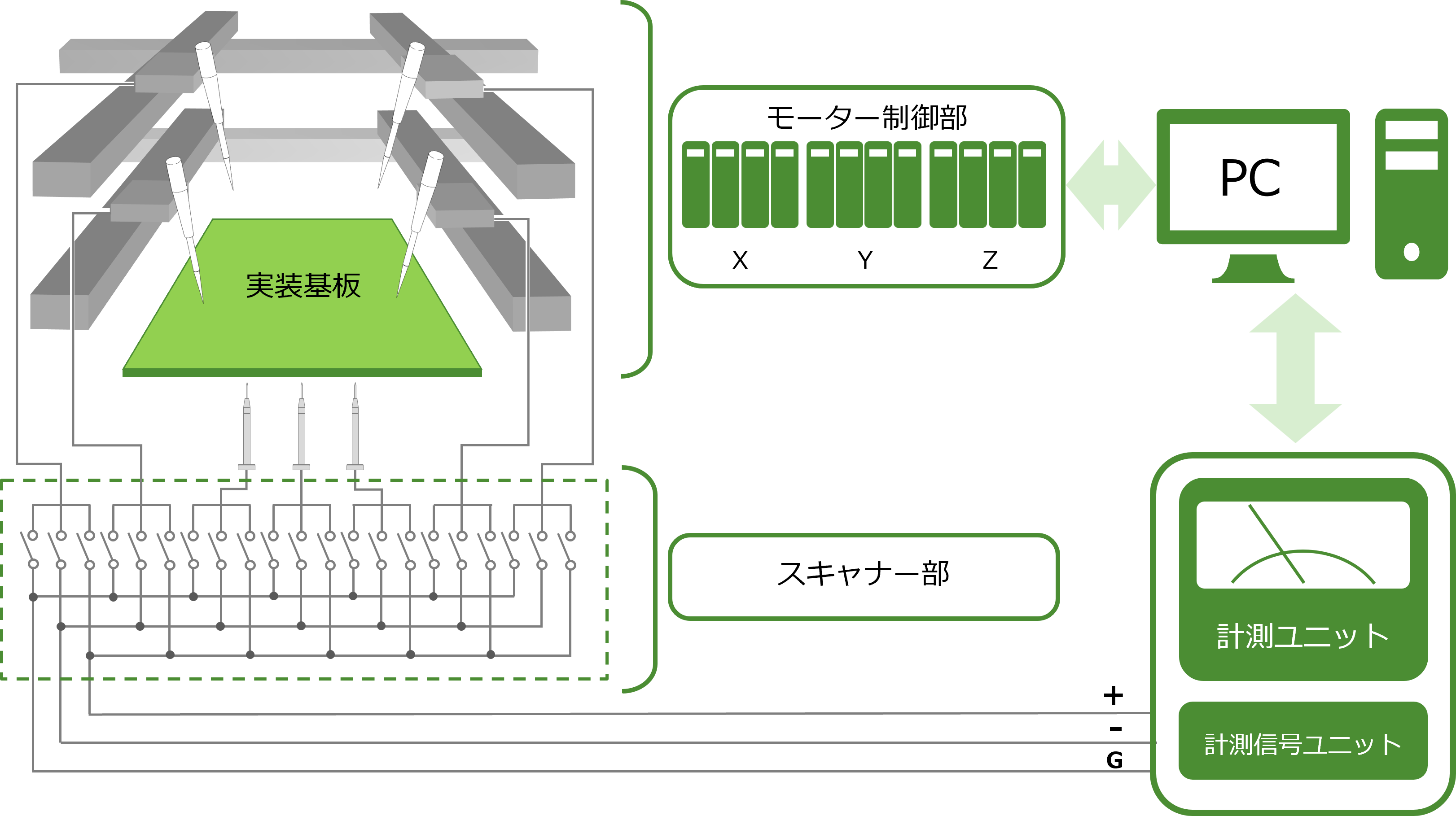
治具式とフライング式の比較
評価項目 | 治具式インサーキットテスタ | フライングプローブテスタ |
---|---|---|
検査準備 | 検査治具製作(検査プログラム作成込み) | 検査プログラム作成 |
検査準備期間 | 15~30日 | 0.5~1日 |
ランニングコスト |
約20~100万円
|
殆ど不要
|
最小プローブ間ピッチ | 1.27mm | 0.15mm |
最小コンタクトパッド | 0.8mm | 0.06mm |
基板の設計変更対応 | 検査治具の再製作が必要 | 検査プログラムの修正・変更で対応 |
基板の誤差・位置ズレ | 対応不可 | 位置補正機能有り |
検査速度 | 平均4~10msec(*調整時間は含まない) | 平均30~60msec |
各種基板検査装置の不良検出能力比較
不良項目 | インサーキットテスト (ICT) |
機能検査 (FT) |
外観検査 (AOI) |
X線検査 (AXI) |
---|---|---|---|---|
欠品 | ◎ | ○ | ◎ | △ |
ハンダブリッジ | ◎ | ◎ | ○ | ◎ |
マイクロブリッジ | ◎ | 〇 | - | - |
部品下面ショート | ◎ | ◎ | - | ◎ |
BGAのボール浮き | ◎ | ○ | - | △ |
ハンダ量(過多・過少) | - | - | ○ | ◎ |
部品定数間違い | ◎ | △ | - | - |
部品特性不良 | ○ | ◎ | - | - |
部品種類違い | ○ | ○ | △ | - |
部品極性違い | ◎ | ○ | △ | - |
回路機能確認 | - | ◎ | - | - |
採用業界・用途
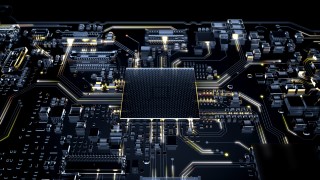
半導体製造装置
半導体製造装置
実績
高密度実装基板の検査
課題
部品間ピッチの狭い箇所は検査治具の製作が難しく、検査できない
メリット
0.15㎜ピッチのプロービングが可能なフラングプローブテスタはテストポイントが無くても殆どの箇所にコンタクト可能。 非常に高いテストカバレッジを実現。
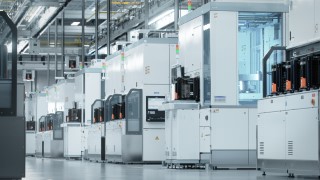
EMS企業
EMS企業
実績
基板試作段階からの電気検査
課題
治具式テスタでは、試作のたびに治具を再作成する必要がある。設計変更時は治具も作り直しとなるためコスト、時間が発生
メリット
仕様変更に即対応して検査、試作レベルから高品質なものづくりが可能。 ハンダ印刷や、リフローでの温度管理が適切かなど、量産へ向けた生産データ確立・検証。 後付部品や部品交換のリワークなどのミスチェック。 試作/量産工程の各種プロファイルが適切かどうかを電気的に確認。
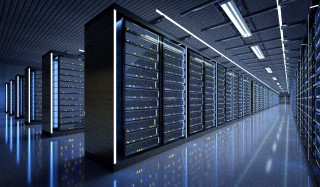
通信インフラ、サーバー
通信インフラ、サーバー
実績
品質要求の厳しい製品向け基板の検査
課題
治具式テスタでは、品目ごとに治具が必要、保管場所の確保や段取りが手間になる
メリット
治具コスト不要、製品立ち上げ時間の短縮等で、少量多品種基板の検査に最適。 部品一点ごとの検査項目・検査内容・検査結果を数値的に判定することで、様々な基板の品質を詳細かつ明確に管理し、不良の流出を防御。他の検査方法に有りがちな、曖昧な検出結果が存在しない。
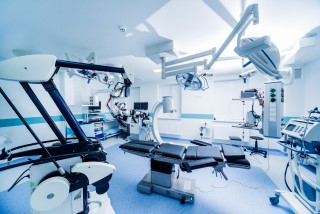
医療機器
医療機器
実績
インラインによる全数検査
3D_AOI(外観検査)との併用
課題
マイクロブリッジなど、AOIでは検知できない不良流出
メリット
AOIでは検出できない不良検査をフライングプローブテスタに移行し併用。 各々の特徴を活かして虚報排除、検査能力の向上とスピードアップを実現。
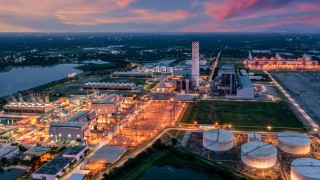
発電・電力システム
発電・電力システム
実績
ディスクリート部品に限定した実装確認
課題
AOIでは検査できないディスクリート部品の品質担保
メリット
電源ラインなどに関わる手挿入部品など、画像検査では検出困難な誤配・ブリッジ・ショート・極性を電気的に検査。 電源通電時の部品破壊・基板破壊を未然に防ぎ、廃棄基板の発生を削減。
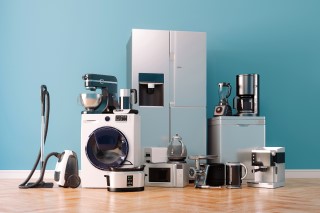
コンシューマー製品
コンシューマー製品
実績
量産型高密度実装基板の機種切換え工程 マウンタのプログラム確認用チップ定数検査
課題
実装工程において、実装機への部品セットミスや実装プログラムミスがあるとロットアウトが発生
メリット
両面テープを貼付したベアボードにチップ部品を仮装着し,チップ部品の電極にコンタクトして定数検査を実行。 人の手作業や目視で行われているチェックが、正確に短時間で可能。
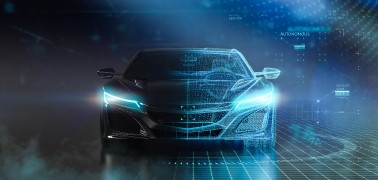
自動車
自動車
実績
不良解析
課題
ファンクションテストで不良判定された基板、市場から故障で返却された基板などの不良解析には、高度な知識が必要
メリット
フライングプローブテスタを使用すれば、不良箇所を容易に発見できる。修理時間の大幅な短縮と、解析不能による廃棄基板の低減を実現。
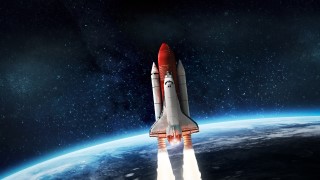
航空宇宙・防衛
航空宇宙・防衛
実績
少量生産基板の検査
課題
治具式テスタでは基板ごとに治具作成が必要、コスト/納期がかかる
メリット
検査プログラムを作るだけで即検査投入でき、AOI・XOI・ファンクションテストだけでは発見できない不良を見つけられるため、少量生産基板でも品質レベルを高められる。 測定値や検査日時などを保存、トレーサビリティ資料として手軽に検索が可能。
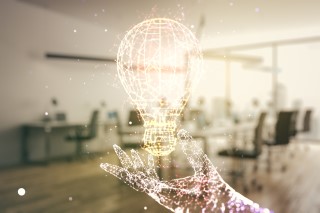
ライティング(LED照明)
ライティング(LED照明)
実績
目視検査→自動検査への置き換え
課題
作業者の負担、判定基準のばらつきが発生
メリット
カラーセンサーによる自動検査で作業者の負担ゼロ。 数値比較による明確な判定基準で安定検査。
開発の歴史と世界展開
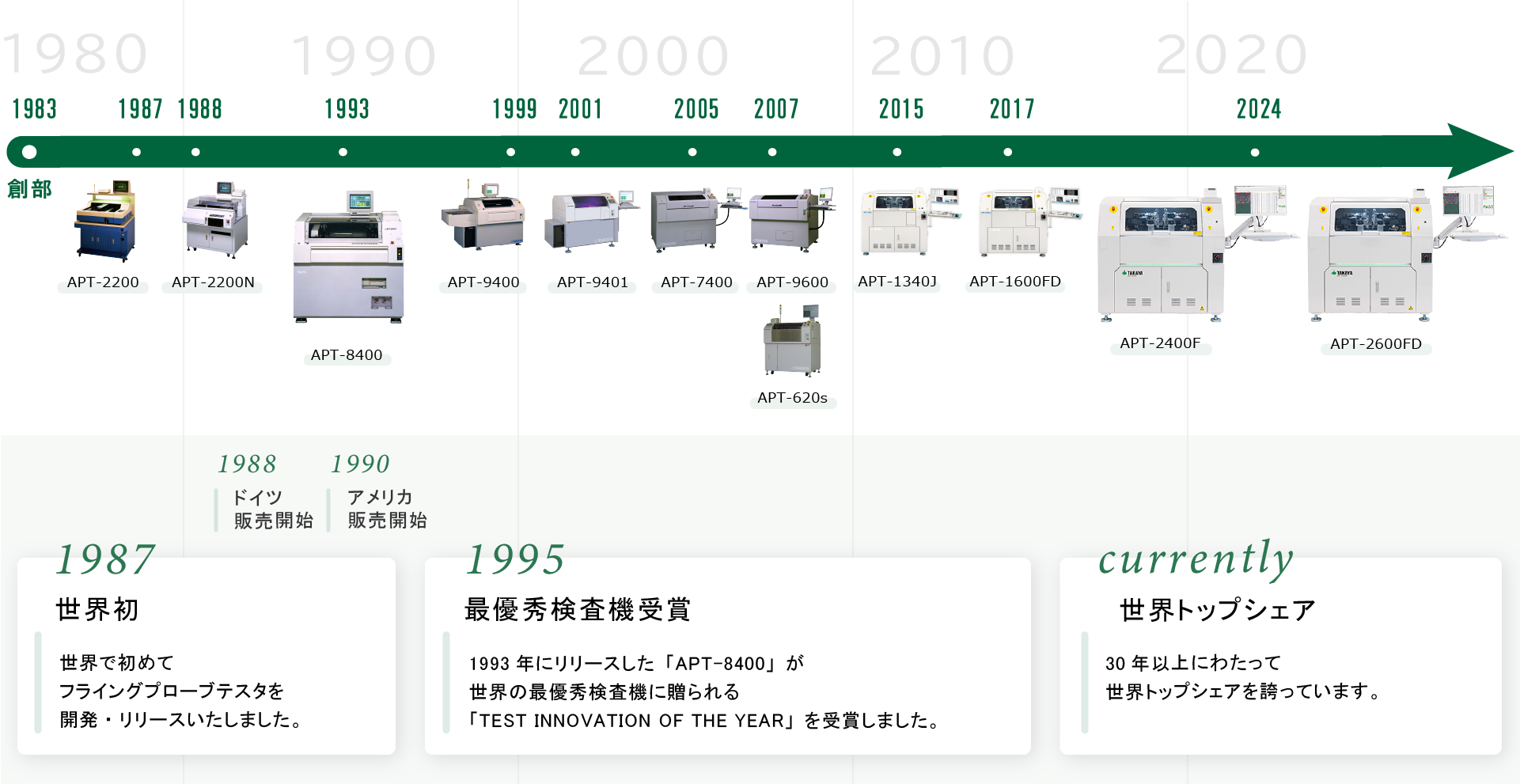
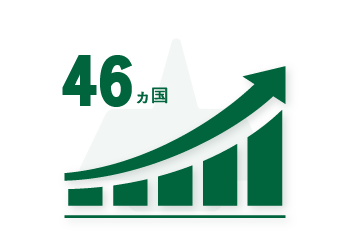
導入実績
46ヵ国以上の導入実績があります。

販売拠点
アメリカ・ヨーロッパ・中国・東南アジア各地に販売拠点を設置しています。
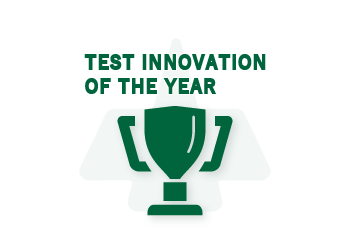
世界で高評価
1995年に「TEST INNOVATION OF THE YEAR」を受賞しました。
タカヤは伊藤忠商事株式会社様と海外販売に関する代理店契約を結んでおります。 世界各国の認定パートナー企業とともに、グローバルでの販売/サポートを行っています。
伊藤忠商事株式会社(itochu.co.jp)
TAKAYA Flying Probe Tester(takaya-itochu.com)
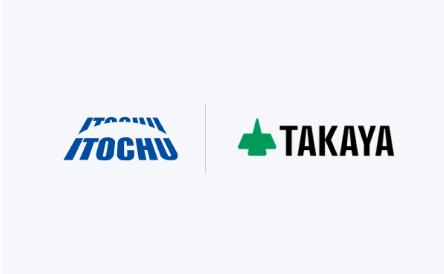
タカヤが選ばれる理由
ノウハウ
タカヤは、1987年に世界初のフライングプローブ・テストシステムを発表しました。 この革新的なシステムは、エレクトロニクス産業のほぼ全分野において、電気検査(インサーキットテスト)の手法を根本から変えました。 少量の試作品から量産まで、様々な基板の検査を高精度かつ低コストで行える仕組みを確立しています。
イノベーション
タカヤは、高品質・技術革新・柔軟性に重点を置いた検査システムを一貫して開発し続けてきました。 現在でも、さらなる検査領域の拡大・検査スピード短縮を目指し、日々新システムの開発に精力的に取り組んでおります。
信頼性
タカヤのテスタは、高い品質管理基準のもとすべて日本国内で製造しています。 装置本体の長期間にわたる精度維持、安定性は、エレクトロニクス産業のあらゆる分野のお客様から高く評価されています。
充実したサポート
設置工事やオペレータへのトレーニング・定期メンテナンス・校正・検査プログラム作成のサポートなど、熟練のサービスマンが対応します。 回路基板検査のスペシャリストとして、エレクトロニクス業界のお客様のパートナーでありたいと考えています。